Researchers at the RIKEN Center for Sustainable Resource Science (CSRS) in Tokyo announced they have created a device that spins artificial spider silk – closely matching the real thing – which could be used for the textile industry. The study was published in January in the scientific journal Nature Communications.
The microfluidic device
Spider silk is a biopolymer fibre made from large proteins with highly repetitive sequences called spidroins; within the silk fibres are molecular substructures called beta sheets, which must be aligned properly for the silk fibres to have their unique mechanical properties.
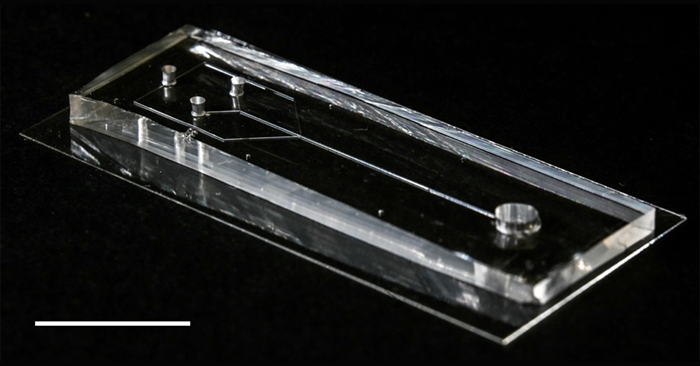
Rather than devising the process from scratch, RIKEN scientists took a biomimicry approach. As Keiji Numata (who led the study) explains, «we attempted to mimic natural spider silk production using microfluidics, which involves the flow and manipulation of small amounts of fluids through narrow channels. Indeed, one could say that the spider’s silk gland functions as a sort of natural microfluidic device».
The device developed by the researchers looks like a small rectangular box with tiny channels grooved into it. Precursor spidroin solution is placed at one end and then pulled towards the other end using negative pressure. As the spidroins flow through the microfluidic channels, they are exposed to precise changes in the chemical and physical environment, which are made possible by the design of the microfluidic system.
The correct conditions
Under the correct conditions, the proteins self-assembled into silk fibres with their characteristic complex structure. The researchers experimented to find these correct conditions and were eventually able to optimize the interactions among the different regions of the microfluidic system.
Among other things, they discovered that using force to push the proteins through did not work; only when they used negative pressure to pull the spidroin solution, could continuous silk fibres with the correct telltale alignment of beta sheets be assembled.
«It was surprising how robust the microfluidic system was once the different conditions were established and optimized» says Senior Scientist Ali Malay, one of the paper’s co-authors. «Fiber assembly was spontaneous, extremely rapid, and highly reproducible. Importantly, the fibres exhibited the distinct hierarchical structure that is found in natural silk fibre».
The ability to artificially produce silk fibres using this method could provide numerous benefits. Not only could it help reduce the negative impact that current textile manufacturing has on the environment, but the biodegradable and biocompatible nature of spider silk makes it ideal for biomedical applications, such as sutures and artificial ligaments.
«Ideally, we want to have a real-world impact» says Numata. «For this to occur, we will need to scale-up our fiber-production methodology and make it a continuous process. We will also evaluate the quality of our artificial spider silk using several metrics and make further improvements from there».